What is a servo motor?
-
Automation
-
Health & wellness
-
Life environment
-
Automotive
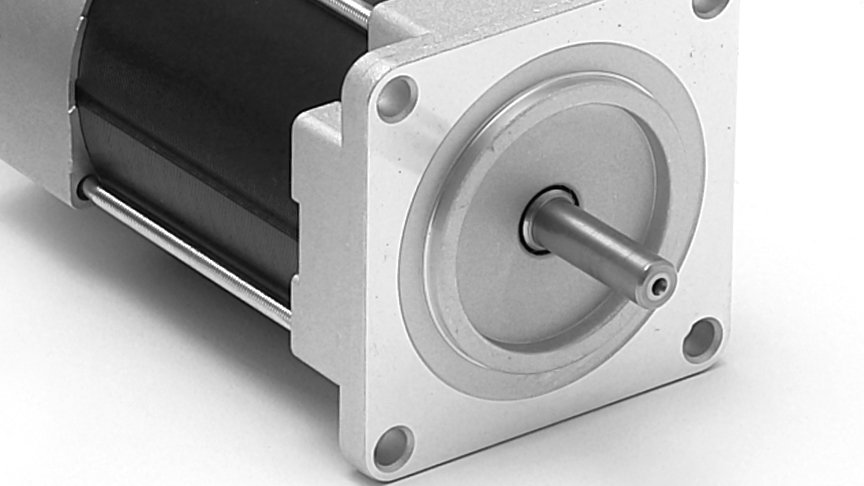
14 Jul. 2020
Whereas common electric motors run continuously and serve as a source of motive power in machinery, servo motors incorporate a control mechanism and are able to rotate by a specified angle and stop at a precise position. These capabilities have led to their use in equipment control in fields as diverse as industry and hobbies, with applications ranging from the positioning of joints in industrial robots to the control of rudder angle on radio-controlled aircraft.
Definition of servo motor
The term "servo" refers to the control mechanism. In terms of technology, the mechanism that performs control is called the "master" and the mechanism being controlled is called the "slave." Both terms, "servo" and "slave" derive from "servus", the Latin word for slave.
In other words, servo motors get their name from the fact that they can be relied upon to operate "exactly as commanded". Any electric motor capable of controlling parameters like position and speed is called a servo motor, regardless of how this control is achieved.
Accordingly, the use of this term sometimes encompasses stepper motors and coreless motors. But, for our purposes here, a servo motor will be defined as a motor that has an encoder (rotational motion detector) together with a driver that uses information from this encoder to control speed and position (rotational angle).
Differences between servo motors and stepper motors
Like servo motors, stepper motors have the ability to control their angle of rotation based on an external input, and therefore are also able to be used for positioning machinery and similar applications. However, these two types of motors differ in the following ways.
Control mechanism
Servo motors have an encoder (rotational motion detector) that can determine their rotational position and use this information to perform feedback control of motor position. This provides precise stopping accuracy and the ability to move back to its original position should motor position deviation occur when stopped. For stepper motors, in contrast, the rotational angle of the motor is proportional to the number of input pulses. Accordingly, the driver controls position based on the number of input pulses it receives from the controller. Although this avoids the need for a position sensor, it also means that there is no way to detect position deviations. Unexpected changes in load, for example, can result in the motor getting out of synchronization (meaning the rotational angle of the motor differs from the angle specified by its input).
Servo motor
Stepper motor
Torque and speed
Servo motors can operate at high speeds and also deliver reliable torque over a wide speed range, from low to high. While stepper motors can deliver high torque at low speeds in particular, their torque diminishes with speed and therefore are not well suited to high-speed operation.
Cost
Because servo motors require a rotary encoder and servo controller (driver), they cost more than stepper motors.
History of servo motors
The technology of servo motors has advanced significantly along with advances in industrial robots.
Interest in factory automation started growing in the United States from the 1950s, initially involving mechanisms such as belt conveyors, automatic machinery, and industrial robots. While early automated machinery and industrial robots tended to use hydraulics or pneumatics to control actuator positioning, they had problems in terms such as accuracy, operational reliability, the associated plumbing, and hydraulic fluid or air leaks.
Subsequently, the use of DC servo motors grew through the 1950s and 60s as their technology improved, and they began to be fitted in industrial robots in place of the troublesome hydraulic and pneumatic mechanisms.
AC servo motors, meanwhile, emerged in the 1980s. Their practical benefits include making robots smaller and lighter, and as a result, they now make up the bulk of servo motors used in modern industrial machinery.
Types of servo motors
Servo motors can be grouped into DC servo motors and AC servo motors
DC servo motors
These are servo motors driven with a brushed direct current (DC) motor. Although DC motors are easier to control than AC motors and were widely used in the past for their small size and low cost, advances in AC motor control technology has seen fewer opportunities for their use in recent times.
AC servo motors
These are servo motors driven with an alternating current (AC) motor. Although their control is more complex than that of DC motors, advances in control technology enabled them now to be the most common type of servo motor.
Depending on their drive mechanism, AC servo motors can be divided into synchronous motors (SMs) and induction motors (IMs). The difference is based on whether or not they have a permanent magnet.
SMs incorporate a permanent magnet. To increase motor output, the amount of permanent magnet usage (which are expensive) increases, and therefore makes them cost more. For this reason, they are widely used for low power applications (up to 10kW). However, with the emergence of high-performance permanent magnets in recent years, synchronous AC servo motors are now the default option.
IMs do not use permanent magnets and tend to be used in higher output applications (10kW or more).
Applications for servo motors
Given their characteristic of accurate positioning, servo motors have a wide range of uses in applications such as industrial robots and precision machinery. Application examples include the following:
- Industrial robot joints
- Humanoid robot joints
- Equipment control in food processing machines
- Equipment control in packaging machines
- Belt drives in conveyor systems
- Automatic doors in trains
- X-Y tables used in LCD and semiconductor inspection machines
- Presses/roll feeders
- Rotating stages for machine tools or inspection systems
- Control of presses
- Control of bonding machines
- Control of plastic molding machines
- Control of amusement machines
- Radio control and other hobby applications
- Coating or vapor deposition machines
- Spin cleaning machines for LCDs and semiconductors
Overcoming your problems with servo motors from ASPINA
ASPINA supplies synchronous (SM) servo motors that use brushless DC motors. By equipping a brushless DC motor or hybrid stepper motor with a rotary encoder, and having the driver perform the required servo control, ASPINA can also supply these as AC servo motors.
ASPINA supplies its servo motors as system products that incorporate drive and control systems as well as mechanical design. These are backed by comprehensive support that extends from prototyping to commercial production and after-sales service.
ASPINA can offer solutions that are tailored to suit the functions and performance demanded by a diverse range of industries, applications, and customer products, as well as your particular production arrangements.
ASPINA supports not only customers who already know their requirements or specifications, but also those who are facing problems at early stages of development.
Do you struggle with the following concerns?
Motor selection
- Don't have detailed specifications or design drawings yet, but need advice on motors?
- Don't have anyone in-house with expertise in motors and can't identify what sort of motor will work best for your new product?
Motor and associated component development
- Want to focus your resources on core technology, and outsource drive systems and motor development?
- Want to save the time and effort of redesigning existing mechanical components when replacing your motor?
Unique requirement
- Need a custom motor for your product, but been declined from your usual vendor?
- Can't find a motor that gives you the control you require, and about to give up hope?
Seeking answers to these problems? Contact ASPINA, we're here to help.
List of the same series columns
- Applications for blower motor
- What is a blower motor?
- Advantages of brushless DC motors over brushed DC motors
- Features and applications of DC motors
- Is this brushless motor cheap or expensive? - What factors determine its price?
- Different types of DC motor and their respective features
- What is a geared brushless DC motor?
- How does an electronic speed controller for a brushless DC motor work? And what should you consider when you choose the right one?
- Small brushless motors
- Difference between brushed motor and brushless motor
- What are the disadvantages of brushless DC motors? And how can they be overcome?
- Advantages of brushless DC motors: How they differ from brushed DC motors
- What is an actuator?
- How do brushless DC motors work? The need for a drive circuit explained
- Do brushless DC motors require a drive circuit? – Controlling brushless DC motors
- What is a brushless DC motor?
- How do brushed DC motors work? The need for regular maintenance explained
- Brushless DC motor applications: examples that demonstrate their features
- Stepper motor applications: Examples that demonstrate their features
- Motors designed for easy control: How do stepper motors work?
- What are the differences between brushed and brushless DC motors?
- What is a PSC motor
- What is a blower?
- What is a DC motor? - features and mechanisms
Contact us for more information
- New inquiry
- Prototype
- Upgrade
- Customization
- Your spec
- Literature
- Support
- Others