New approach to balance quality, cost, and delivery for small space satellites - 6 Reaction Wheels
-
Space
-
Small satellite, CubeSat
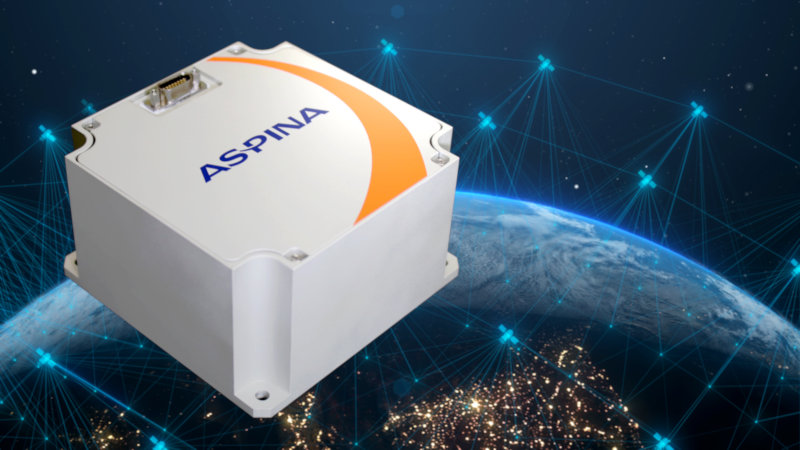
ASPINA’s reaction wheels for small space satellites
ASPINA is developing a lineup of reaction wheels (RWs) for small satellite constellations, a network of many satellites, in low earth orbit (LEO). Currently the lineup consists of RWs for 3 different satellite sizes: (1) 100 kg-class satellites, (2) 200 kg-class satellites, and (3) 10 kg-class CubeSats. In response to customer requests, we have started development of high-torque reaction wheels, and are also considering RWs for 300kg class to 500kg class satellite to our lineup. These RWs are designed with competitive cost and shorter lead time.
The RW for 100 kg-class small satellites, cylindrical in shape with a diameter of about 10 to 25cm, reduces the effects of disturbance torques and has the environmental durability required for satellite components.
We are able to develop RWs with reasonable cost and short lead time by leveraging ASPINA’s many decades of supply chain expertise and experience with automotive- and consumer-grade parts while ensuring quality for new satellite applications.
Reaction wheel sample for a 100 kg-class satellite
Small satellite manufacturers seek components with fast delivery at a reasonable price
Many satellite constellations have been proposed and developed in the last decade. ASPINA has studied the market and interviewed experts from the small satellite industry and satellite development start-ups in Japan and the United States. Kody Ichiki, Chief Engineer of New Business Development in ASPINA's Development Engineering Division, says, "As short mission life operations and constellations has become mainstream, the quality, performance, and cost requirements for satellites has shifted away from those of large stand-alone satellites designed for long mission lifetimes." With global rocket payload capacity rapidly increasing, the number of satellites is expected to also rapidly increase making the mass production of more complex satellite components economically viable for the first time in history.
Small satellite manufacturers need to source parts and components that fit those conditions. However, our market study has shown that there are very few RWs available on the market that can be supplied quickly and at an appropriate price, even though the RW is a key component of a satellite.
The RW mainly consists of a flywheel, an electric motor, and a control board. Due to the conservation of angular momentum, the reaction caused by varying the rotation speed of the flywheel applies a rotational force to the satellite to control its attitude, the orientation of the satellite or direction it is pointing.
Behavior of reaction wheel
ASPINA's reaction wheel with consumer-grade parts achieves quality for small satellite operation
The Development Engineering Division of ASPINA launched a team in 2019 to develop RWs, covering responsibilities from market research to prototyping and testing.
It is important for satellite manufacturers to reliably procure the components they use in large quantities with short lead times so that they can manufacture more satellites faster. To meet their requirements, ASPINA is developing RWs that can be shipped within 2 to 3 months after receiving a purchase order, by using consumer-grade products such as electronic components widely available in the market. In addition, we select parts that can withstand the vibration, shock, temperature, vacuum, and radiation conditions of space and launch operations and evaluate them through in-house testing. Regarding Ichiki’s plan for component selection, "we are going to create ASPINA's own evaluation criteria to match the quality level unique to small satellites."
The vibration of the RW is a source of on-board disturbance that affects satellite observation and communications. Suppressing this disturbance requires precisely balancing the flywheel. Therefore, we needed to design a new measurement jig to achieve the necessary level of precision. In addition, we employ bearings specially designed for high precision products and optimize the control methods to ensure stable rotation. These countermeasures make the vibration magnitude much smaller than conventional electric motors.
The RW for 100kg-class satellites is a cylindrical wheel with a diameter of about 10 to 25cm. In order to obtain sufficient strength for its small size and light weight, we performed various structural analyses and designed the whole structure to withstand vibrations and shock during launch.
The table below is the major developing specifications of RWs for space satellite:
Item | Developing specification | |||||
---|---|---|---|---|---|---|
Model | ARW-3m | ARW-0.35 | ARW-1A | ARW-1B | ARW-2 | ARW-20 |
Satellite mass | CubeSat | 100kg class | 200kg class | 200kg class | 300kg class | 500kg class |
Maximum angular momentum | 0.003Nms | 0.35Nms | 1Nms | 1Nms | 2Nms | 20Nms |
Maximum output torque | 1mNm | 15mNm | 100mNm | 30mNm | 100mNm | 200mNm |
Mass | 72g | 1kg | 1.5kg | 1.5kg | 1.9kg | 6kg |
Envelope | 30 x 30 x 28mm | 100 x 100 x 80mm | 140 x 140 x 50mm | 150 x 150 x 80mm | 140 x 140 x 65mm | 250 x 250 x 120mm |
Operating temperature range | -30 to 70°C | -20 to 50°C | -20 to 50°C | -20 to 50°C | -20 to 50°C | -20 to 50°C |
Radiation (TID) | 30krad | 20krad | 20krad | 20krad | 20krad | 20krad |
Supply voltage | 9V to 12V | 18V to 34V | 18V to 34V | 24V to 34V | 18V to 34V | 28V to 34V |
Maximum power consumption | 2.5W | 15W | 100W | 42W | 100W | TBD |
Control mode | Speed or torque | Speed or torque | Speed or torque | Speed or torque | Speed or torque | Speed or torque |
Command/Telemetry | I2C | RS485 | RS485 | RS485 | RS485 | RS485 |
Mission life | 2 years | 5 years | 5 years | 5 years | 5 years | 5 years |
*Above specifications are under development and subject to change.
We are developing the RW for 100kg-class satellites jointly with AXELSPACE Corporation, a manufacturer of small satellites in Japan. This development project was selected by the New Energy and Industrial Technology Development Organization, a government research institute of Japan, as part of its R&D program for FY2020 Space Industry Technology Information Infrastructure Improvement under the theme of "Development of low-cost, quick-delivery RWs for the expansion of the small satellite market."
We are also working on the development of a smaller RW for CubeSats. We are carrying out this development by participating in a project of Ark Edge Space Inc. adopted by the Ministry of Economy, Trade and Industry of Japan for the FY2021 Space Utilization Promotion Research and Development (development of fundamental technologies related to small satellite constellations (orbit and attitude control technologies)).
Creating a reaction wheel lineup to meet diverse needs for satellites
"We expect the market of small satellites, especially the ultra-small CubeSat and small satellites up to several hundred kilograms class, will grow rapidly" says Ichiki. ASPINA is developing a lineup of RWs to meet a variety of needs, including satellite size and application.
The development of ASPINA’s RW is a boost to the construction of satellite constellations from the component level. We also believe that this will provide more opportunities to create businesses that utilize satellite constellations and, as a result, contribute to better quality of our everyday lives through innovative applications in disaster management, adherence to environmental regulation, agriculture, urban development, transportation, and distribution network management.
Choose ASPINA's reaction wheels for your success in the space business.